Research theme
Hybrid Rocket Propulsion
The RFD is the only university laboratory in West Japan that has an academic environment to develop and fire hybrid rocket (HR) engines (as of April 2020), and our facilities are currently being expanded as our research progress. It is possible to set up innovative research as an undergraduate or graduate dissertation topic and make results (see rearch achivements). Depending on the students' efforts, they can present their results at international conferences as well as at domestic ones, write peer-reviewed papers as the first author, or apply for patents. We are looking forward to the paritcipation of highly motivated students challenging academic research on chemical rocket propulsion.
*Although it is possible for students of the Department of Space Systems Engineering to join our lab, please note that since this laboratory belongs to the Department of Mechanical and Control Engineering, most of the students are from the Deppartment of Mechanical and Control Engineering.
We have received many grants and external funding and have a wide variety of laboratory equipment such as
- a high-pressure oxygen gas feed systen up to 10 MPa
- an engine thrust measurement system
- a compact color high-speed camera (ISO speed of 16,000, max 540,000fps)
- a dual-head FDM 3D printer
- a 3D scanner
- a small machining workshop including milling machine, lathe, drilling machine
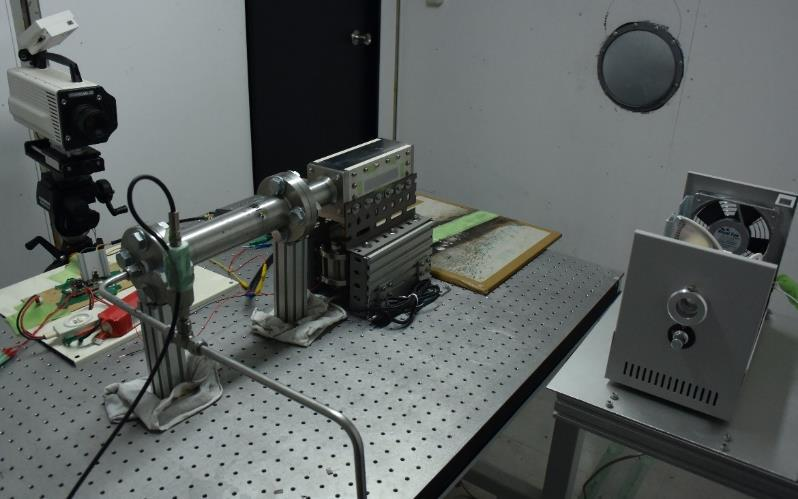
Combustion experiment room
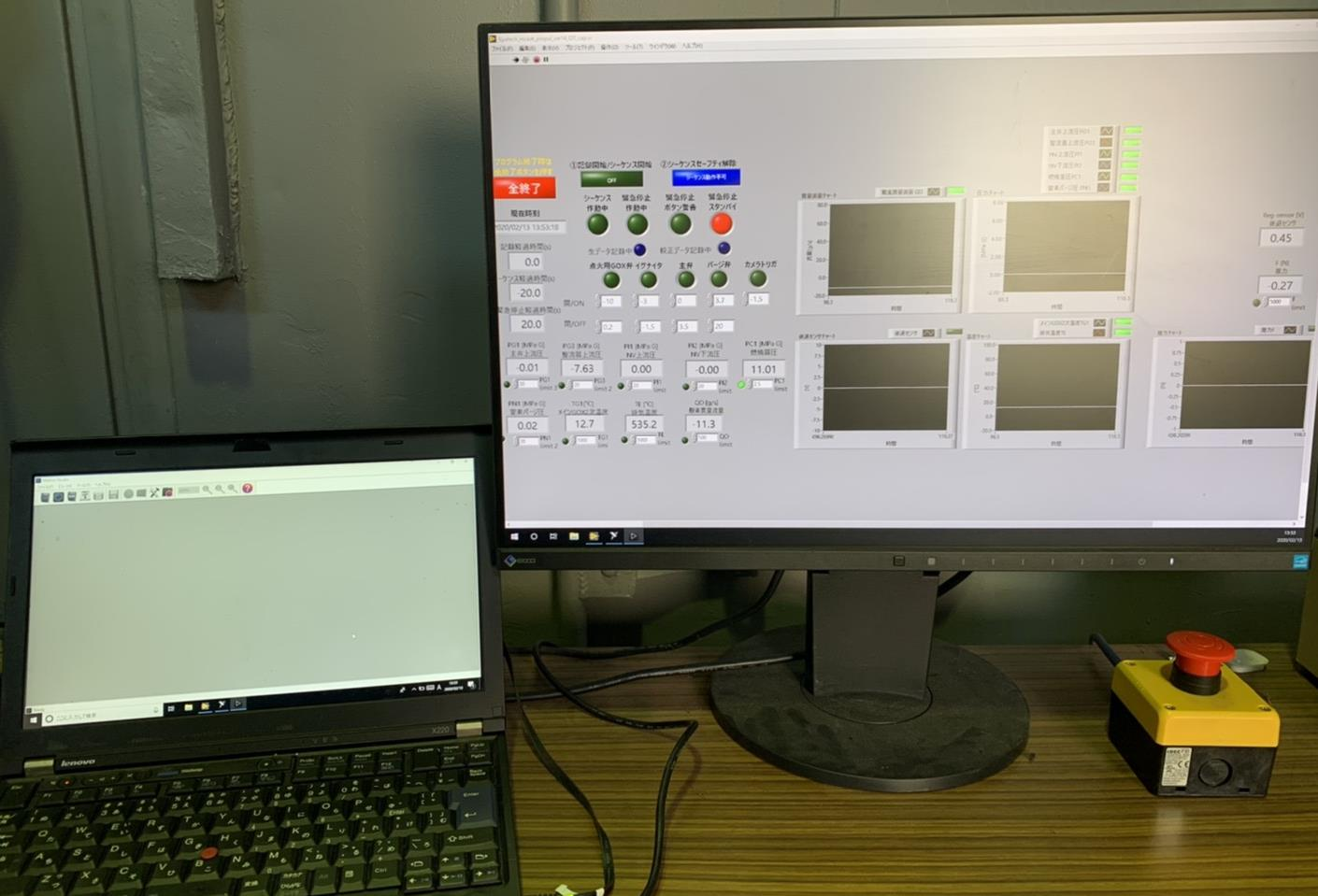
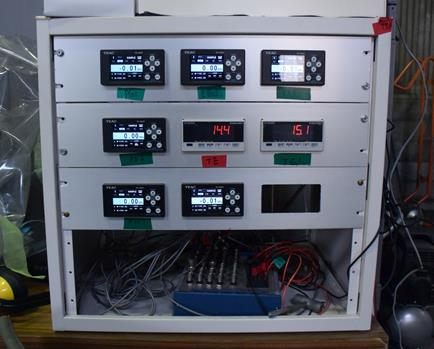
Engine Measurement and Control System
What is Hybrid Rocket Propulsion?
“Hybrid Rocket Propulsion” refers to chemical rocket propulsion in which a fluid oxidizer is injected into a solid fuel enclosed in a motor case. HR is propelled by a high-temperature product gas generated by diffusion combustion in the boundary layer formed near the solid fuel is injected from a nozzle.
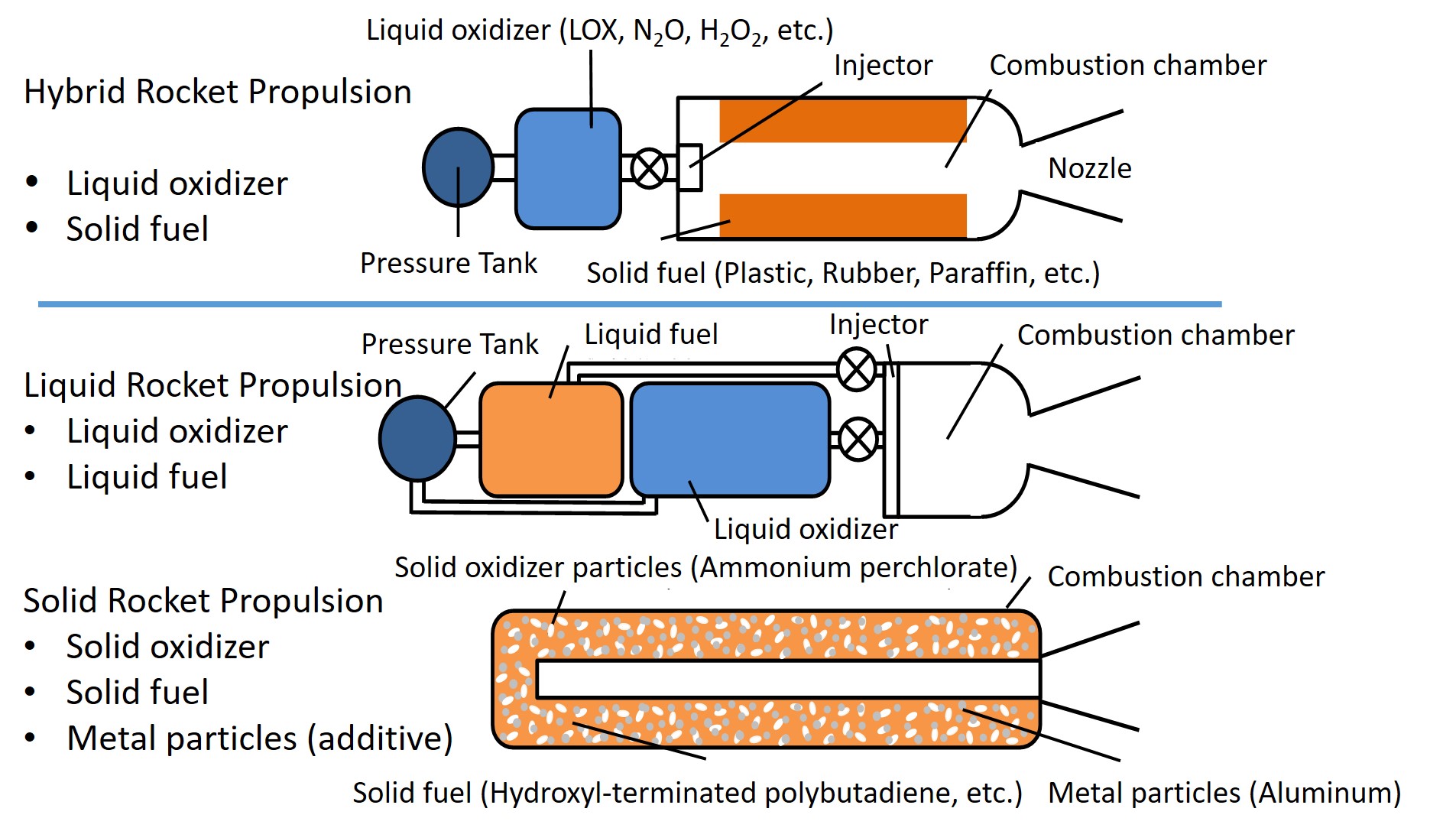
Comparison of Hybrid rocket with other chemical rocket propulsion
Advantages of Hybrid Rocket Propulsion
1. Non-explosuve chenucak rocket propulsion that is less likely to continue unintended burns.
2. Non-toxic propellant combinations can be selected for both the reactants and the products.
3.Thrust modulation and re-ignition are possible by controlling the oxidizer flow.
These advantages significantly reduce the design, manufacturing, and operational constraints of space systems associated with the risk of unintentional destructions or pollutions compared to conventional rocket propulsion. This can result in a huge cost reduction of the total cost from development to operation. It is also expected to be put to practical use as a chemical propulsion system with a large thrust-to-weight ratio in situations where safety is required without damaging people or other equipment.
Applications of Hybrid Rocket
The applications of HRs widely range from education and hobby to space travel. Model rocket systems for the education and hobby, represented by the HyperTEK system, are available for sale. In Japan, it is used by amateur rocket teams such as those of university students. Several organizations have also launched HR engines developed by them. In recent years, Scaled Composites developed the SpaceShipOne using a HR engine, which was the first commercial repetitive ballistic manned spacecraft and won the Ansari X Prize. Ballistic space travel will be commercialized by its successor, SpaceShipTwo. Applications are also being considered for nano-satellite launchers and nano-satellite propulsion systems. There are a few start-up companies in Taiwan, Germany, the United States, and other parts of the world.
Challenges for Practical Application
1. Conventional solid fuels have a low fuel regression rate (fuel volume flow rate per fuel unit surface area), which leads to a low thrust-to-weight ratio for a single port cylindrical fuel grain when assuming a practical aerodynamic and structural design as a launch vehicle.
2. The actual combustion efficiency tends to be low.
3. There are dispersions in regression rates because the heat of combustion is transported through the turbulent boundary layer to the solid fuel.
4. Thrust control and the 3rd problem cause a residual propellant remaining in the rocket without burning, which reduces the acceleration performance of the rocket.
5. There are no real-time methods that measured fuel flow rates during an actual rocket flight.
The first and second problems had been studied for many years as important issues for practical application compared to the others, and it was found that they can be greatly improved by changing the injection method of the oxidizer, the solid fuel composition, and the shape of the combustion chamber. However, when applied to a launch vehicle with severe delta-v requirements or thrust control including fuel flow rates, the 3rd to 5th problems need to be solved.
Research Themes
Our laboratory is working on the following research topics to solve 3rd to 5th problems.
• Fuel regression and liquefied flow characteristics of wax-based fuels under various acceleration environment considering during a powered flight
• R&D of solid fuels with real-time fuel regression measurement function using multi-material 3D Printer and conductive filament
• Advanced thrust and mixture ratio feedback control of hybrid rocket engines(starting from 2020)
In addition, it is possible to advise investigations on engine thoretical performance and flight simulations utilizing our research achivements on these topics.
Fuel regression and liquefied flow characteristics of wax-based fuels under various acceleration environment considering during a powered flight
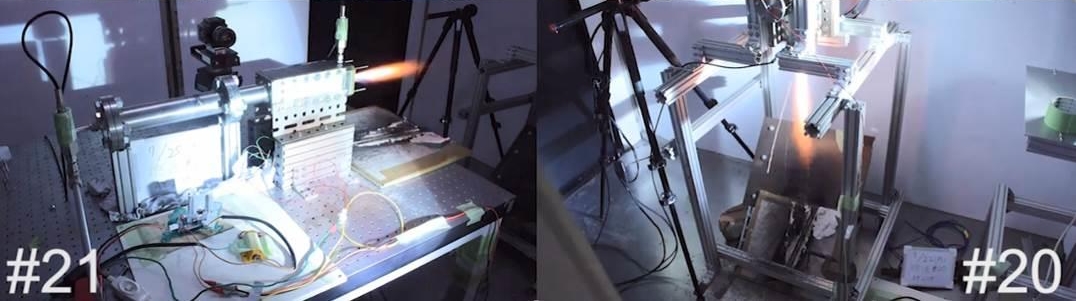
Experiment for visualization of solid fuel flow in horizontal and vertical position of wax fuel

Visualization of roll-waves of liquefied wax-based fuels: the world’s first visualization of the roll-waves that develop into fuel droplets entrained into the gaseous flow in a combustion flow field.
We also conduct combustion visualization experiments in a high-acceleration environment using the rocket thread of the Aerospace Plane Research Center at the Muroran Institute of Technology.
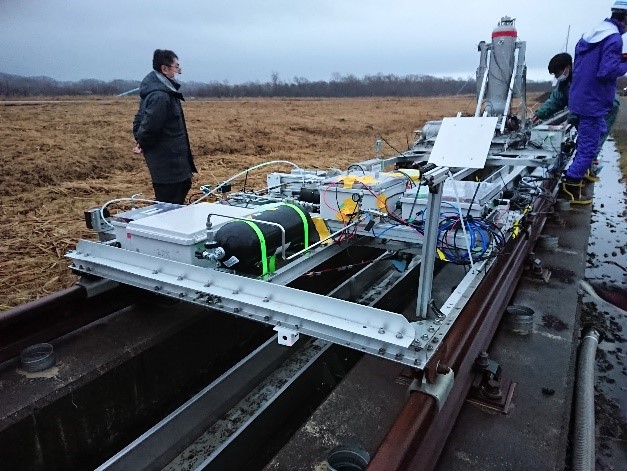
Experimental setup of conbustion visualization connected to the rocket sled main frame.

A test on the rocket sled system at Muroran Institute of Technology
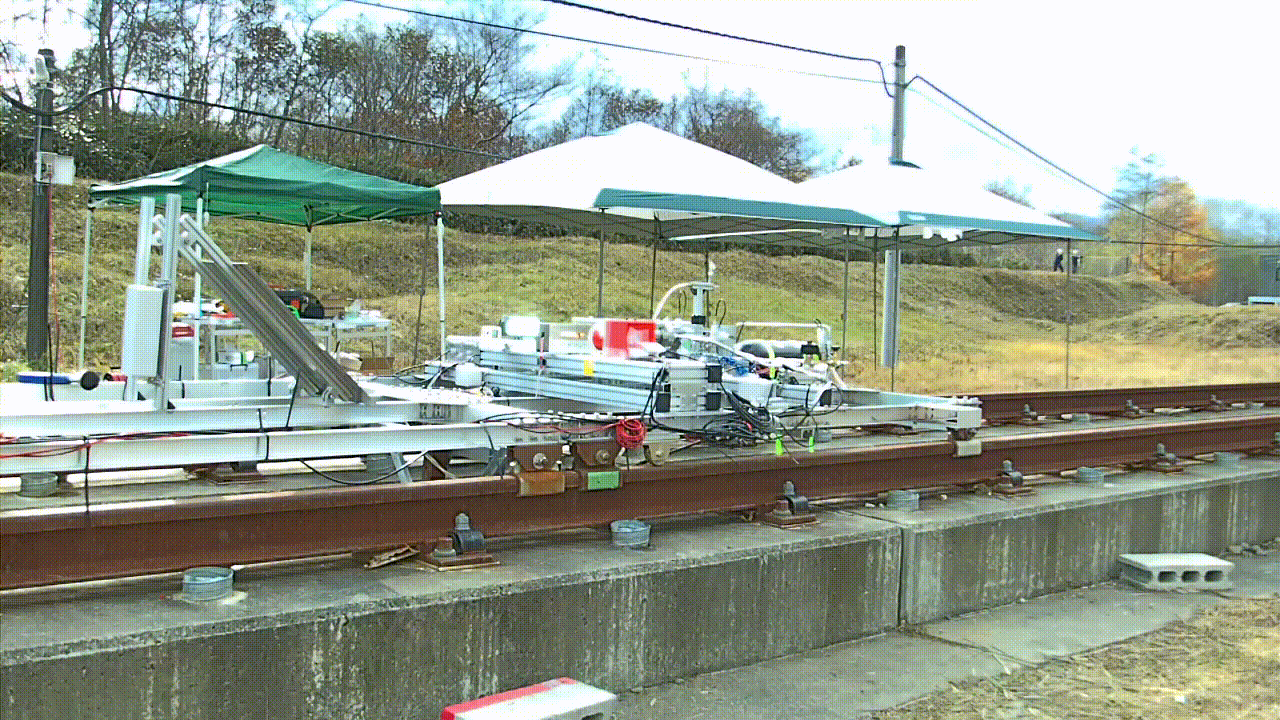
Running test of the rocket sled
R&D of solid fuels with real-time fuel regression measurement function
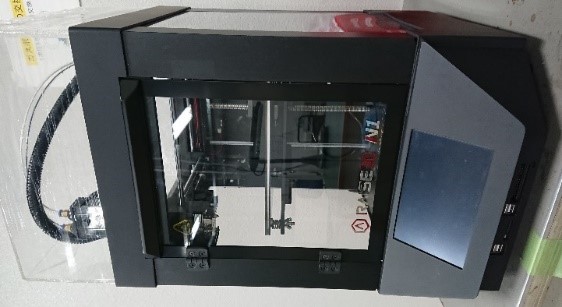
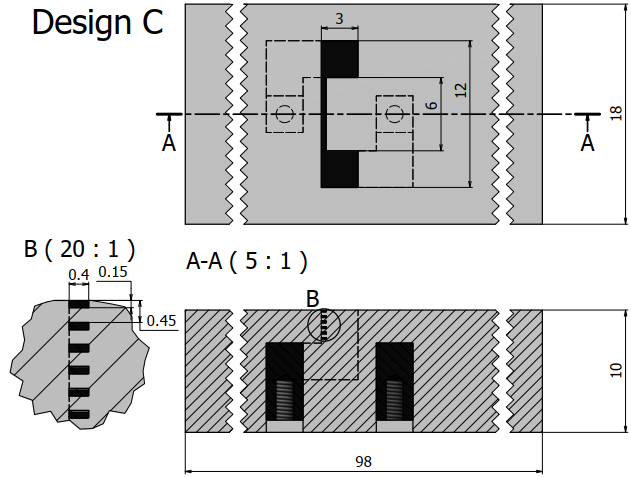

Left: Dual-head 3D printer (Two types of filaments can be used for modelling)
Right: A prototype solid fuel design with a ladder-shaped resistor structure
Below: A cylindrical solid fuel design with a ladder-shaped resistor structure

A prototype solid fuel (After a burn)

A cylindrical solid fuel (After a burn)
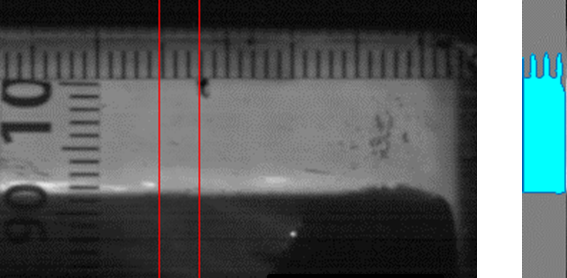
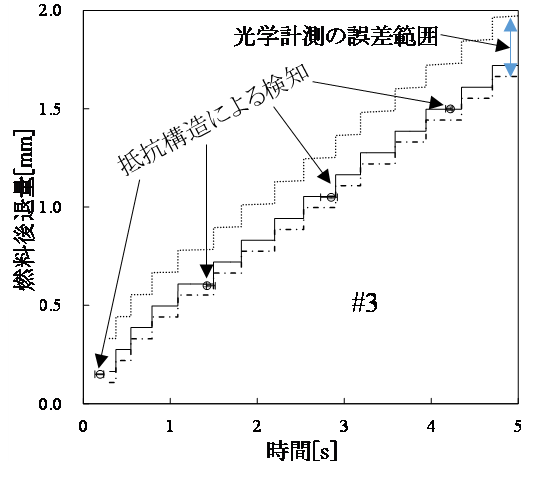
Left: Visualization of the fuel regression surface.
Center: Image recognition of the fuel surface by binarization.
Right: Time-trace of fuel regression surface measurement with the resistor structure of the fuel with that from the visualization image recognition for comparison
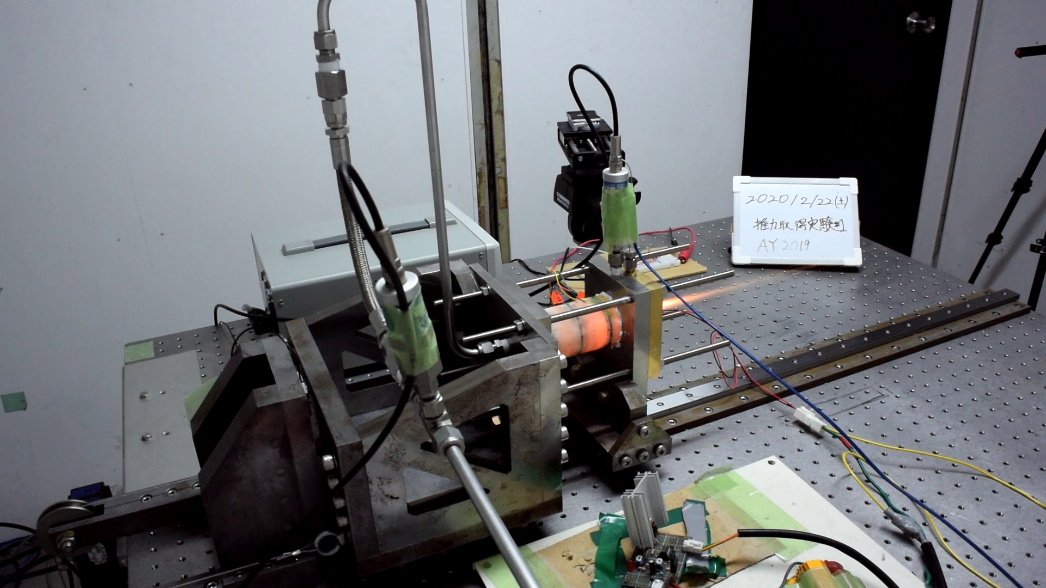
Functional test of a 3D-printed solid fuel and thrust measurement system: a test to use a coated FDM solid fuel also as a combustion chamber

Combustion test of 3D-printed cylindrical solid fuel.
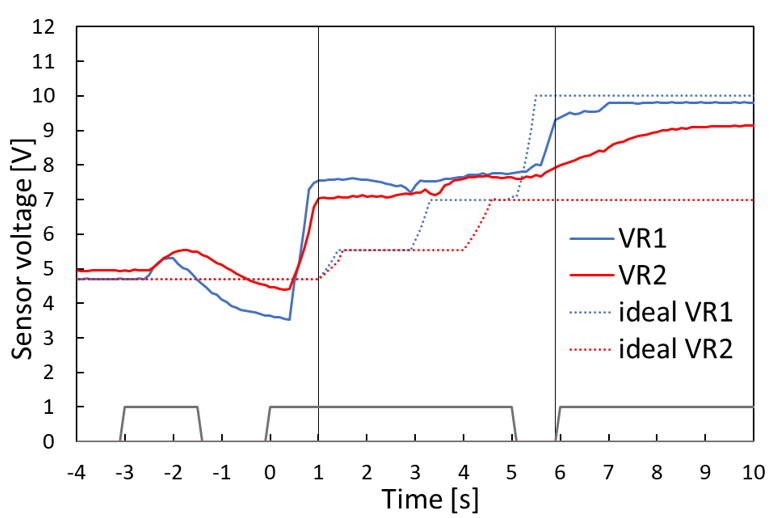
Comparison of voltage change in circuit structure and ideal voltage change calculated from regression rate.